Injection Molding
Cost-effective series production using injection molding.
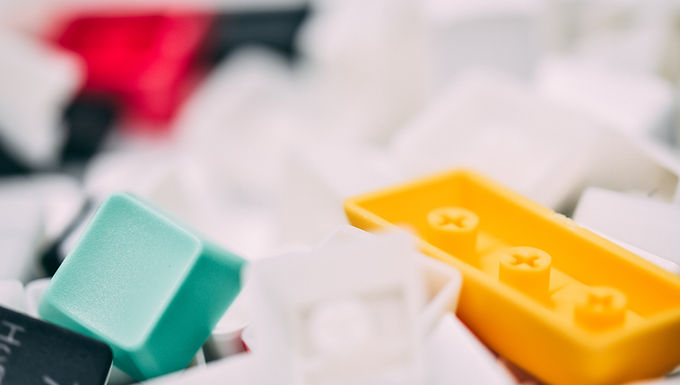
Injection molding is the manufacturing process of choice for the cost-effective production of small and large series. We offers a wide range of plastics, resins and metal with the suitable strength and surface quality for your components.
How does injection molding work?
First, the raw material, consisting of plastic granules or powder, is liquefied by heating. The liquid plastic is then injected under high pressure into metal injection molds (also called a cavity), usually made from steel or aluminum. After the melt has hardened in the mold, it is opened and the finished plastic part can be removed. The finished parts can then be further refined; common processes include polishing, painting, electroplating and laser marking.
Although capable of producing a wide range of parts, injection molds have some design constraints. Plastic injection molded parts must have narrow walls. They should avoid overhanging features and have some degree of draft (tapered sides) so that the molded part can be ejected from the mold.
Injection molding is principally used with plastics and thermoplastics in particular. Thermoplastics are polymers that soften at an elevated temperature (at which point they can be freely injected into a mold) and then return to a solid state after cooling. Injection molding also works with thermosets, which can be cured to make a solid but cannot then be melted back into a liquid. Less common are elastomers.
Rigid Plastic Materials:
ABS, ASA, CA, HDPE, LCP, LDPE, PA 6, PA 6/6, PARA, PBT, PBT-PET, PC, PC-ABS, PC-PBT, PC-PET, PCT, PE , PEEK, PEI, PE-PP, PE-PS, PES, PET, PLA, PMMA, POM, PP, PPA, PPS, PS-PPE, PSU, PVC, PVDF, SAN, TPO, TPU.
Elastomer and Rubber Molded Materials:
EPDM, PEBA, PVC, TPE, TPU, TPV, LSR.
Finishing Options
Polishing, Pad printing, Silk screening, Custom color painting, Laser finishing, Heat staking, Texture finishing.
A wide variety of industries benefit from the highly versatile process of injection molding, including:
Medical & Pharmaceutical, Eletronics, Construction, Food & Beverage, Automotive, Toys, Agriculture, Consumer Goods, Sporting Goods.
Our Injection Molding Capabilities
Custom Plastic Injection Molding Services
The most popular custom injection molding process, thermoplastic, is suitable for consumer products, automotive components, and many other applications.
Liquid Silicone Rubber Molding Services
Liquid silicone injection molding is ideal for creating detailed, temperature-resistant parts from thermosets liquid silicone, either alone or in conjunction with overmolding.
Metal Injection Molding Services
Suitable for small and detailed metal parts, metal injection molding is cost-effective in large volumes and wastes less material than CNC machining.
Injection Molding Processes
Custom Plastic Injection Molding
Steel tooling with rapid lead times, ideal for prototyping, design validation, and bridge production.
Overmolding
Rubber or silicone molding over an existing plastic part.
Insert Molding
Plastic injection molding around a preformed, often metal threaded, insert.
Secondary Operations
Heat Staking
The process of locally heating a plastic component in order to reform and insert another component (such as a threaded insert).
Laser Engraving
Engraving text or a design with the use of a laser.
Pad Printing
A process to apply an ink-based, 2D design to a 3D surface.
Painting
Primer and top coat; standard colors or Pantone matching; masking available; EMI (copper) paint.
Ultrasonic Plastic Welding
A high frequency welder generates heat to join or reform thermoplastics.
How long an injection mold can last depends on several factors:
mold material, number of cycles, operating conditions, and time between production runs. The life expectancy of an injection mold can range from 1M+ cycles to less than 500 cycles based on the above criteria.